Capabilities
Our core capabilities are underpinned by an innovative, solution-led approach to research and testing.
We research and develop real-world solutions and products that are scalable across different-sized structures.
We welcome any conversations to discuss how we can help you.
Active vibration control
Active vibration control works by measuring the vibrations in a structure (typically with an accelerometer), processing these measurements in real-time and using these to drive a force aimed at cancelling out whatever force caused the vibrations in the first place.
The technology is similar to that used in noise-cancelling headphones where microphones (instead of accelerometers) measure noise (instead of vibrations) and a loudspeaker generates an “anti-noise” signal (rather than a counterbalancing structural force).
VES research focusses on controlling vibrations experienced on lively floors, footbridges or entertainment venues.
In 2014 we developed the world's first permanent installation for active control for concert induced floor vibrations. The knowledge gained from this has allowed us to develop a robust implementable control system for human-induced vibrations in civil structures.
Active vibration isolation
Active vibration isolation involves isolating very sensitive pieces of equipment from a more noisy vibration environment. Examples include medical imaging devices, which could malfunction as a result of vibration levels even below the human perception threshold.
Passive vibration control
Tuned mass damping systems
Tuned mass damping systems are an example of passive vibration control. These systems are installed within a structure and dissipate energy to reduce vibration levels.
We have designed and built tuned mass damping systems to mitigate against human-induced vibrations in structures from large pedestrian footbridges to domestic properties. We can create bespoke systems, from initial assessment through design, manufacture and validation.
Find out more about our equipment on the Structures Laboratory webpage.
Forced vibration testing
Forced vibration testing uses measurable and controllable forces to generate a dynamic response in a structure, then uses experimental modal analysis to estimate modal parameters: i.e. natural frequencies, damping ratios, mode shapes and modal masses.
Shakers
Shakers use accelerometers to measure a structure's acceleration, which can be used to calculate the force it is subjected to.
Hammers
Hammers contain a load cell that directly measures the force applied when a structure is struck.
Sensors
We use a combination of wired and wireless sensors deployed across a structure to record synchronised dynamic response.
Ambient vibration testing
Ambient vibration testing uses unmeasured environmental dynamic loads - such as wind, traffic or ground borne vibration - to generate broadband dynamic response. Then operational modal analysis is used to estimate natural frequencies, damping ratios and mode shapes.
Vision based measurement system
This system is used for monitoring large structures and tracking how they move in the long term. It combines machine vision cameras and mathematical algorithms.
Accelerometers
Our highly sensitive accelerometers are used to measure ground-based vibrations that are too small for humans to notice.
Sensors
We use a combination of wired and wireless sensors deployed across a structure to record synchronised dynamic response.
Monitoring systems
Our monitoring systems enable us to set up operator-free, intelligent data processing and reporting.
Distributed monitoring
We have developed a unique set of wireless, synchronised acceleration recorders that can be deployed across a structure. Although the sensors are separate units, synchronising them at the beginning of testing gives us a unique capability to monitor very large structures such as tall timber buildings and long-span bridges. The sensors can also be used to monitor inside structures and between closed rooms.
Remote monitoring
We deploy remote monitoring systems in harsh environments, including offshore structures such as wind turbines and lighthouses.
We have helicopter-trained staff and equipment ready to be deployed at short notice.
VES are registered in regulatory databases to enable access to numerous sites and infrastructures both on and off shore.
Datasets and results analysis
We hold extensive data drawn from a wide range of global infrastructure.
By analysing our own data, and that provided by clients, we can interpret patterns and provide real-world predictions of vibrations or structural issues.
Find out more about our equipment on the Structures Laboratory webpage.
Custom design and manufacturing
Hardware and software
We can provide custom-made monitoring systems that can interface with a wide variety of sensors as needed for your project, including:
- accelerometers
- strain gauges
- displacement transducers
- temperature and humidity sensors.
3D design, print and manufacture
We build prototypes from concept through to final design, using facilities for 3D design, 3D printing, and fabrication.
VSimulators
The £4.8m EPSRC-funded VSimulators is a unique state-of-the-art facility combining a motion platform, virtual reality and motion capture technology. The facility will enable us to replicate vibration environments that are encountered in real life, from offices in tall buildings that sway under wind loading, to sports stadia where crowds jump up and down. It will enable us to explore the level at which vibrations can be perceived by humans and what are acceptable levels that might be used in design.
Visit the VSimulators website »
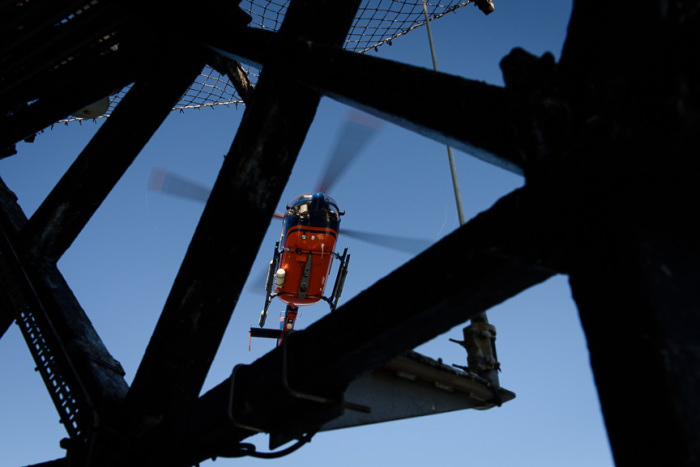
More information
-
Consultancy and industry: Find out more about how we can help you and how to get in touch
-
Research: Meet our academic staff and view their research profiles